Every time you pick up a beverage, take off your shoes or play with a toy, you’re using a plastic product made through the process of injection molding.
Plastic moulding techniques are very versatile and can be used for many applications. But with all of the options, there are some things you should know before choosing a particular method. Contact American Plastic Molds now!
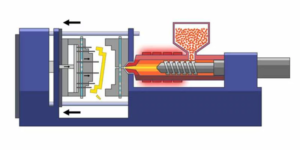
The injection moulding process can be used to produce a wide variety of parts. Some common examples include plastic containers, everyday items like toothbrushes and pens, and garden products such as plant pots that can replace terracotta pots for less cost. The injection moulding process is highly repeatable and can be used to produce a large number of identical parts quickly. It also allows designers to incorporate a variety of features directly into the product itself. This can include hinges, fasteners and specialized surface textures.
The primary advantage of injection molding is its ability to produce complex shapes and structures with a high level of precision. It is also a highly efficient and cost effective method for production of small to medium runs of parts. This is due to the rapid cycle times and short manufacturing lead times resulting from this technique.
A critical factor in the success of injection molded parts is the proper design of the mold. This includes consideration of draft angle (a taper applied to vertical walls) and wall thickness. The draft angle is designed to assist in releasing the part from the mould. A minimal draft angle is 2 degrees but larger angles may be required for taller features. The wall thickness is important as non-uniform walls can cause warping or sink marks when the melted plastic cools down. This is avoidable by ensuring that the wall thicknesses are uniform and that thick sections are avoided wherever possible.
There are tens of thousands of different materials that can be used in injection moulding, including most thermoplastics and some thermosets. Selection is based on the strength and function needed for the final part as well as the manufacturing costs. These can be further enhanced by mixing different materials, alloys or blends to achieve a particular set of properties.
During the injection molding process, the injected plastic is heated to a very high temperature before it enters the mould cavity. This is accomplished using an electric hot-plate or a hydraulic press. The injection pressure is proportional to the projected area of the part, and this is multiplied by a clamp force that ranges from 2 to 8 tons per square inch.
Rotomoulding
Rotomoulding is a hollow-structure plastic manufacturing process that uses a lot of heat and low pressure. It starts by loading a powdered polymer into a hollow mould, which is then sealed and heated. Once the molten resin has cooled, it lines the interior of the mould, forming the desired shape. Then, the mould is cooled again, and the finished product can be removed from the mould.
Because rotomoulding does not use pressure, it can produce large parts with very precise dimensions and wall thicknesses in relatively small batches. However, it is a slower process than injection and blow molding. Moreover, it requires careful design of the mould to ensure that the polymer adheres and solidifies properly. This makes it unsuitable for high volume production.
The process also involves a cooling cycle that may take up to ten minutes. This is because the cooling must be done slowly to prevent warping of the new rotomolded part. To avoid this problem, it is important to use a circulating fan that can dissipate the heat evenly.
Another consideration in the rotomoulding process is the ability of the chosen plastic to resist oxidation in the molten state. The oxidation process can cause the degradation of the plastic’s physical properties and chemical structure. To prevent this, a rotomolded product should be designed with a seam in an area that is not critical or visible.
As with other types of moulding, rotomoulding produces durable and versatile products that can withstand a range of temperatures and environmental conditions. It is particularly useful in the agricultural industry, where it can be used to create a variety of items such as cattle feeders and fertiliser tanks. Rotomoulded products are lightweight and can be easily transported, which is a great advantage for farmers who need to move their livestock over long distances.
Rotomoulded furniture and homewares are becoming increasingly popular. The process allows designers to create unique shapes and designs that would not be possible with other materials, and it can be used to manufacture a wide range of products from vases to bathtubs. The resulting products are strong, lightweight and resistant to corrosion and other chemicals.
Extrusion
Plastic extrusion is a mechanical industrial process that uses pressure and thrust to give polymer materials the desired shape. It is an efficient, cost-effective way to produce a wide range of products and components. The extrusion process begins by loading plastic pellets into a hopper. These are then conveyed to a heated barrel where they are melted and then forced through a die. The die’s shape determines the final product’s dimensions and characteristics. The die is also responsible for regulating the flow of material and maintaining consistency in production.
After passing through the die, the molten plastic is cooled so it retains its shape. This can be achieved by running it through water for tubing and pipes or through cooling rolls or fans for thinner products like films. This is a critical step because it ensures the final product has the correct density and strength for its intended use.
Unlike injection molding, which is suited for high-volume production runs, extrusion is best used for producing longer, continuous parts. However, it can be limiting in its ability to create complex cross-sectional profiles. Additionally, it is not ideal for creating parts with varying thickness. This is because the temperature of molten plastic can change its properties as it cools.
When choosing a plastic for extrusion, it is important to consider its ductility, strength, thermal properties, and melting point. These factors will affect the resulting part’s performance, cost-efficiency, and quality. The type of die used is another key consideration. The size and shape of the die can have a significant impact on production speeds and the amount of heat needed to melt the plastic.
The environmental footprint of extrusion is also a crucial factor for many companies. By using eco-friendly materials and integrating renewable energy sources into production, manufacturers can minimize their carbon emissions and contribute to a greener production process.
Blown film extrusion is a popular process that produces flexible plastic films. It involves the use of a flat die and an air-filled ring that pushes molten plastic outward to a specific width and film thickness. The plastic is then cooled and stretched by rollers, which help to regulate the film’s thickness. This type of extrusion is often used for packaging and tubing that require barrier properties. Coextrusion is a variation on this process that combines multiple layers of different materials to produce a multi-layered product with a variety of desirable qualities.
Sheet moulding
Sheet molding compound (SMC) is a high-strength and lightweight material that is used in the production of composite products. It consists of several essential ingredients, including resins, fiberglass, catalysts, and fillers. Its popularity in molding applications is due to its superior strength-to-weight ratio, insulation properties, and corrosion resistance. In addition, it can be easily molded into complex shapes with high-level of precision and accuracy.
This material is commonly found in automotive parts, as it provides a durable and cost-efficient alternative to metals for car exteriors. It is also used in marine and aviation industries for components such as fuel tanks, fuselages, and interiors. Compared to traditional metals, SMC is lighter and has better energy efficiency.
SMC manufacturing involves the application of heat and pressure to a charge of resin-filled glass or carbon fiber. The process produces a quality part that is highly durable and has an excellent surface finish. It is also easy to repair. In addition, it is easy to use and produces less waste. This technology is highly cost-effective, especially in large-volume manufacturing scenarios.
The main ingredient of SMC is the thermosetting resin matrix, which is a cross-linked polymer, usually made from polyester, vinyl ester, or epoxy. The matrix is then reinforced by long strands of glass or carbon fibers. These long fibers add to the material’s tensile and flexural strengths. SMC’s high tensile and flexural strengths make it a viable alternative to metals for car body panels.
Various additives can be added to SMC to improve its performance and appearance. Fillers reduce the weight of the material, while stabilizers help to prevent shrinkage. Thickeners improve the flowability of the SMC during the molding process and prevent the formation of pinholes. Additives can also include pigments, release agents, and corrosion inhibitors.
A measured amount of resin paste is released onto a plastic carrier film by the Paste Reservoir. The film is then passed under a chopper, which cuts the fiberglass and carbon fibers into smaller pieces. The chopped fibers are then rolled into sheets and stored in rolls at a pre-determined thickness.